
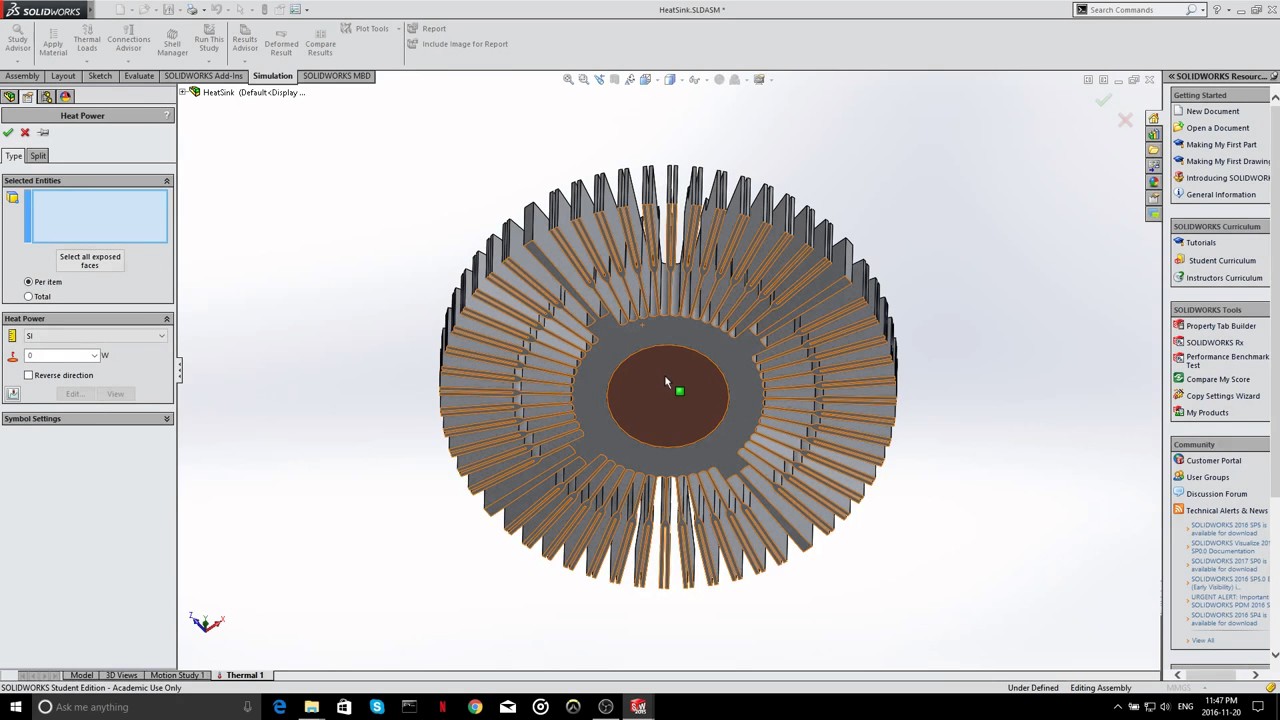
- Solidworks flow simulation 2015 tutorial upgrade#
- Solidworks flow simulation 2015 tutorial full#
- Solidworks flow simulation 2015 tutorial professional#
Solidworks flow simulation 2015 tutorial upgrade#
For more complex fluid analysis you can upgrade to SOLIDWORKS Flow Simulation.
Solidworks flow simulation 2015 tutorial full#
Unlike the full version, SOLIDWORKS Flow Simulation, the Xpress version is specifically designed to analyze fluid flow in a fully enclosed volume that includes at least one inlet and one outlet. Based on the calculated velocity field, you can find problem areas in your design and improve them before you manufacture any parts.
Solidworks flow simulation 2015 tutorial professional#
These settings are of most importance after this and generally govern the size of our problem more than the basic mesh.Have you tried SOLIDWORKS FloXpress? It is a fluid dynamics add-in application included with SOLIDWORKS Standard, Professional and Premium, that calculates how fluid flows through part or assembly models. Settings related to the model geometry are controlled to transform this from the basic mesh into the initial mesh of the problem. There is not much to the basic mesh other than these settings. A -3 ratio in the x-direction means that moving in the x-direction, the largest cell will be closest to the origin and the smallest cell, which is three times smaller than the largest one, will be further down the x-axis. Negative ratios mean the cells shrink in the direction of the axis. A ratio of two would mean the largest cell in that interval is twice as wide as the smallest.

The ratio tells how large the largest cell is compared to the smallest.
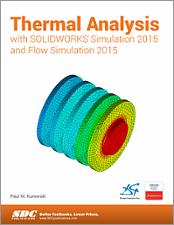
The goal of nested iterations is to get a. The problem with transient flow is that you have to follow the changing flow field, said Derbal. Since large elements right next to much smaller ones is bad, transition sizes are necessary. Using nested iterations, SOLIDWORKS Flow Simulation can solve the same problem with larger time steps, thereby reducing overall computational time. In this case, the ratio represents the distribution of cell sizes in a given interval. The number of cells is easy to understand, but the ratio is not as clear. In the image above, setting values are shown to the right, such as the number of cells and the ratio of that control interval. The image below shows an example of control plane usage. Some reasons are high-interest areas requiring more accuracy, time efficiency of analysis, and proper cell alignment with a particular face to minimize partial and/or irregular cells. There are many reasons why these control planes are useful. Inserting control planes using the “Add Plane…” button seen in the image above allows control of different regions around the model to have varying size cells. To control certain regions of the basic mesh, control planes can be used. At this screen, it is possible to more accurately control the size of the cells in the x-, y- and z- directions by setting how many of them span across those directions. All the other options on this screen are related to transforming the basic mesh into the initial mesh.Ĭlearing the “Automatic settings” checkbox at the bottom, this screen changes to the image below. Sliding it to a lower setting makes the basic cells larger and sliding it to a higher setting make the cells smaller. Only one item on the above screen is related to the basic mesh setting and that is the level of initial mesh slider (the bar with the red and green). Let’s look at the automatic settings screen first. To set this up, there are multiple settings related to it. It only sets its size based on the computational domain and ignores the model shape.
